High Feed Milling Tools
High Feed Milling Tools Market Segments - by Product Type (Solid Carbide High Feed Milling Tools, Indexable High Feed Milling Tools, HSS High Feed Milling Tools, Ceramic High Feed Milling Tools, Diamond High Feed Milling Tools), Application (Aerospace, Automotive, Die & Mold, General Machining, Medical), Distribution Channel (Direct Sales, Indirect Sales), Material Type (Carbide, High-Speed Steel, Cermet, Ceramic, Diamond), and Region (North America, Europe, Asia Pacific, Latin America, Middle East & Africa) - Global Industry Analysis, Growth, Share, Size, Trends, and Forecast 2025-2035
- Report Preview
- Table Of Content
- Segments
- Methodology
High Feed Milling Tools Market Outlook
The global High Feed Milling Tools market is projected to reach approximately USD 5.4 billion by 2035, growing at a compound annual growth rate (CAGR) of around 7.5% from 2025 to 2035. This growth is propelled by advancements in machining technologies that require high efficiency and precision in manufacturing processes. The rising demand for high-performance tooling solutions across various industries, including aerospace and automotive, significantly contributes to the market expansion. Furthermore, the increasing trend toward automation in manufacturing, combined with the growing focus on reducing operational costs and improving productivity, is expected to fuel the adoption of high feed milling tools. As industries evolve, there is a notable shift from traditional machining methods to advanced techniques, driving the need for innovative tooling solutions that enhance machining capabilities.
Growth Factor of the Market
The High Feed Milling Tools market is poised for significant growth, driven by several key factors. One of the primary growth drivers is the increasing demand for precision machining in various sectors, including aerospace, automotive, and medical applications, which necessitate the use of high feed milling tools for efficient material removal. Additionally, advancements in materials science have led to the development of high-performance cutting tools that offer enhanced durability and cutting speeds, making them attractive to manufacturers looking to optimize production processes. Furthermore, the growing trend of automation and digitalization in manufacturing is encouraging the adoption of sophisticated milling tools that can integrate with modern CNC machines, thereby improving productivity and operational efficiency. The push towards sustainable manufacturing practices is also a significant factor, as companies seek tooling solutions that minimize waste and energy consumption. Overall, these interconnected trends are set to drive the growth of the High Feed Milling Tools market significantly.
Key Highlights of the Market
- The market is expected to reach USD 5.4 billion by 2035.
- Projected CAGR of 7.5% from 2025 to 2035.
- Significant demand from aerospace and automotive sectors.
- Growing adoption of automation and digitalization in manufacturing.
- Development of advanced materials enhancing tool performance.
By Product Type
Solid Carbide High Feed Milling Tools:
Solid carbide high feed milling tools are renowned for their exceptional hardness and wear resistance, making them ideal for high-speed machining applications. They are often used in industries that require precision and durability, such as aerospace and automotive. These tools provide superior cutting performance, allowing manufacturers to achieve tighter tolerances while reducing cycle times. The solid construction ensures that they remain stable during operation, which leads to enhanced surface finishes on machined components. Moreover, advancements in carbide technology have allowed for the development of tools that can withstand higher temperatures and pressures, further increasing their efficiency in demanding machining environments. As manufacturers look to optimize production processes, solid carbide high feed milling tools are becoming increasingly popular across various sectors.
Indexable High Feed Milling Tools:
Indexable high feed milling tools are designed for flexibility and efficiency, featuring a modular design that allows for easy replacement of cutting inserts. This versatility makes them an attractive option for machining different materials and shapes, particularly in dynamic production environments. They are often used in heavy machining applications where the speed of material removal and cost-effectiveness are critical. The ability to quickly swap inserts minimizes downtime, making these tools ideal for high-volume manufacturing scenarios. Furthermore, indexable tools are typically engineered to provide excellent chip control, which is essential for maintaining optimal machining conditions and extending tool life. As industries continue to seek solutions that enhance productivity, the demand for indexable high feed milling tools is expected to grow steadily.
HSS High Feed Milling Tools:
High-speed steel (HSS) high feed milling tools are widely recognized for their cost-effectiveness and versatility. They are suitable for a range of applications, from general machining to more specialized uses in industries such as die and mold fabrication. HSS tools are characterized by their ability to withstand high temperatures without losing hardness, making them an excellent choice for various machining processes. While they may not offer the same level of performance as carbide tools, HSS tools are often preferred for their affordability and ease of sharpening, which can reduce overall tooling costs. As manufacturers increasingly look for ways to balance performance with budget constraints, HSS high feed milling tools are likely to occupy a significant share of the market.
Ceramic High Feed Milling Tools:
Ceramic high feed milling tools are gaining traction due to their ability to withstand extreme cutting conditions, making them particularly effective for hard materials. Their high resistance to wear and thermal shock enables them to operate at elevated cutting speeds, which is advantageous in high-production environments. These tools excel in applications that involve machining of hard metals, ceramics, and composite materials, which are common in the aerospace and automotive industries. As manufacturers are constantly pushing for increased productivity and reduced machining times, the demand for ceramic high feed milling tools is expected to rise. Furthermore, ongoing innovations in ceramic materials are likely to enhance the performance characteristics of these tools even further, solidifying their position in the market.
Diamond High Feed Milling Tools:
Diamond high feed milling tools represent the pinnacle of cutting tool technology, primarily due to their unparalleled hardness and wear resistance. These tools are particularly useful for machining abrasive materials and are used extensively in industries such as semiconductor manufacturing and advanced materials processing. The superior cutting performance of diamond tools allows for incredibly fine finishes and high precision, making them indispensable in applications where the quality of the finished product is paramount. Despite their higher price point, the longevity and performance of diamond high feed milling tools justify the investment for many manufacturers. As industries continue to evolve and demand tighter tolerances and higher production rates, the adoption of diamond high feed milling tools is anticipated to grow significantly.
By Application
Aerospace:
The aerospace sector remains one of the most demanding applications for high feed milling tools due to its stringent requirements for precision and material performance. Components in this industry often require complex geometries and high-performance materials that can withstand extreme conditions. High feed milling tools enable manufacturers to achieve the necessary tolerances while minimizing cycle times, thereby enhancing overall productivity. As the aerospace industry continues to expand, driven by increasing air travel and advancements in aircraft technology, the demand for specialized high feed milling tools tailored for aerospace applications is expected to rise accordingly. The focus on weight reduction and fuel efficiency in aircraft design further emphasizes the need for innovative tooling solutions in this sector.
Automotive:
In the automotive industry, high feed milling tools are crucial for the efficient machining of various components, including engine blocks, transmission housings, and other critical parts. The automotive sector is characterized by its need for rapid production cycles and high precision, making high feed milling tools essential for meeting these demands. The continuous push for lighter, more fuel-efficient vehicles has led to an increased focus on advanced materials, which in turn drives the need for specialized cutting tools that can handle these tougher materials. As automotive manufacturers increasingly adopt automation and advanced manufacturing techniques, the reliance on high feed milling tools is expected to grow, resulting in a robust market outlook for this application segment.
Die & Mold:
Die and mold applications utilize high feed milling tools to create intricate shapes and designs with high precision. These tools are particularly beneficial in the production of molds for plastics, metals, and other materials used in various manufacturing processes. The ability to achieve fine details and smooth finishes is essential for ensuring the quality of the final products. As industries continue to demand more complex designs and shorter production times, the importance of high feed milling tools in the die and mold segment is projected to increase. Furthermore, the trend towards additive manufacturing and the use of advanced materials are expected to further drive innovation in die and mold machining, enhancing the role of high feed milling tools in this market.
General Machining:
General machining encompasses a wide range of applications across different industries, making high feed milling tools a versatile choice for manufacturers. These tools are utilized in various processes, including milling, drilling, and turning, to produce components with varying specifications. Their ability to perform efficiently across different materials and geometries makes them a staple in many machine shops. As manufacturers continue to seek solutions that enhance productivity and reduce machining times, the demand for high feed milling tools in general machining applications is expected to witness steady growth. Additionally, the increasing trend towards customization and small-batch production is likely to further elevate the role of high feed milling tools in this segment.
Medical:
The medical industry relies heavily on high feed milling tools for the precision machining of components used in medical devices and equipment. The stringent standards for quality and precision in this sector necessitate the use of high-performance tooling solutions that can meet these requirements. High feed milling tools are particularly advantageous for machining materials like titanium and stainless steel, which are commonly used in medical applications due to their biocompatibility and durability. As the medical device market continues to grow, driven by technological advancements and an aging population, the demand for high feed milling tools tailored for medical applications is expected to increase significantly. Furthermore, ongoing research and development in this field will likely lead to innovations that enhance the performance and efficiency of these tools.
By Distribution Channel
Direct Sales:
Direct sales channels play a crucial role in the High Feed Milling Tools market, as manufacturers often prefer to purchase tools directly from suppliers to ensure quality and performance. This approach allows for better communication between buyers and sellers, facilitating customized solutions that meet specific machining needs. Direct sales also enable manufacturers to benefit from technical support and after-sales services, which are essential for optimizing tool performance and extending tool life. As the market continues to evolve, the trend towards direct sales is expected to grow, with suppliers focusing on building strong relationships with key customers and providing tailored solutions to enhance customer satisfaction.
Indirect Sales:
Indirect sales channels, including distributors and retailers, are also significant in the High Feed Milling Tools market. These channels provide manufacturers with access to a broader range of products and brands, allowing them to choose tools that best fit their requirements. Distributors often offer additional services, such as inventory management and technical support, which can be beneficial for smaller manufacturers that may not have the resources to engage in direct purchasing. The indirect sales route is particularly valuable for companies looking to expand their reach and improve market penetration, as it enables them to tap into established distribution networks. As competition increases, the role of indirect sales channels is expected to remain vital for the growth of the high feed milling tools market.
By Material Type
Carbide:
Carbide is one of the most commonly used materials for high feed milling tools, known for its hardness, wear resistance, and ability to maintain cutting edge integrity at elevated temperatures. Carbide tools are particularly advantageous in high-speed machining applications, where prolonged tool life and consistent performance are critical. The manufacturing of carbide tools involves advanced processes that combine tungsten and carbon, resulting in a composite material that offers superior cutting capabilities. The increasing demand for precision and efficiency in machining processes is driving the growth of carbide high feed milling tools across a multitude of industries. As technological advancements continue to emerge, manufacturers are likely to innovate further in carbide tool design and production methods to enhance performance and reduce costs.
High-Speed Steel:
High-speed steel (HSS) is another prevalent material used in the production of high feed milling tools, valued for its balance of performance and cost-effectiveness. HSS tools are widely utilized for general machining applications and are particularly favored in environments where tool longevity is essential but high-performance machining isn't the primary focus. These tools can maintain their hardness at elevated temperatures, albeit not as effectively as carbide tools, which makes them suitable for a variety of machining tasks. The adaptability of HSS allows manufacturers to use these tools in different machining settings, contributing to their enduring popularity. As market demands shift towards more efficient processes, HSS tools will continue to play a significant role in the overall high feed milling tools market.
Cermet:
Cermet materials, composed of ceramic and metallic components, are increasingly being used in high feed milling tools due to their unique combination of properties. These materials offer excellent wear resistance and toughness, making them suitable for machining abrasive materials. Cermet tools can operate effectively at high cutting speeds, which is a considerable advantage in industries that require rapid production cycles. The demand for cermet tools is expected to rise as manufacturers seek to minimize tool wear and improve machining efficiency. Ongoing advancements in cermet formulations will likely lead to enhanced performance characteristics, solidifying their position in the high feed milling tools market as industries continue to prioritize efficiency and cost-effectiveness.
Ceramic:
Ceramic materials are recognized for their exceptional hardness and thermal resistance, making them an ideal choice for high feed milling tools used in extreme cutting conditions. These tools are particularly effective for machining hard metals and materials that require precision. The unique properties of ceramics enable them to maintain sharp cutting edges for extended periods, which is crucial in high-speed machining operations. The growth of the ceramics market is closely tied to the demand for high-performance tools across various industries, including aerospace and automotive. As manufacturers increasingly adopt advanced materials to enhance performance and efficiency, the use of ceramic high feed milling tools is expected to grow, especially in applications requiring superior performance under extreme conditions.
Diamond:
Diamond, known for its unparalleled hardness, is increasingly being used in high feed milling tools, particularly for machining abrasive materials. Diamond tools excel in applications that require extremely fine finishes and high precision, making them indispensable in high-tech manufacturing sectors such as semiconductor production and advanced materials processing. The longevity and performance capabilities of diamond tools can justify their higher cost, as they often result in lower overall machining costs due to reduced tool wear and increased production efficiency. As industries continue to innovate and push the boundaries of material science, the demand for diamond high feed milling tools is anticipated to rise significantly, reinforcing their position in the competitive landscape of high feed milling tools.
By Region
The North American region is anticipated to hold a significant share of the High Feed Milling Tools market, driven by the presence of advanced manufacturing industries and a strong focus on innovation. The U.S. accounts for a substantial portion of the market, with the automotive and aerospace sectors being the primary consumers of high feed milling tools. The region's CAGR is projected at approximately 6.5% from 2025 to 2035, reflecting the ongoing investments in automation and advanced machining technologies. Furthermore, as companies in North America increasingly prioritize precision engineering and efficiency, the demand for high feed milling tools tailored to meet these needs is expected to rise.
In Europe, the High Feed Milling Tools market is also witnessing robust growth, supported by a strong manufacturing base, particularly in countries like Germany, Italy, and France. The region is known for its emphasis on quality and precision in manufacturing, which drives the demand for advanced tooling solutions. The ongoing transition towards sustainable manufacturing practices and the adoption of digital technologies are further bolstering the market outlook in Europe. As European manufacturers seek to enhance productivity and reduce operational costs, the adoption of high feed milling tools is expected to remain strong, contributing to the overall growth of the market.
Opportunities
The High Feed Milling Tools market presents numerous opportunities for growth and innovation, driven by several factors. One significant opportunity lies in the increasing trend towards automation and Industry 4.0 practices. As manufacturers seek to optimize their production processes, the integration of advanced technologies such as robotics and AI in machining operations opens avenues for the development of high feed milling tools that can deliver enhanced performance and adaptability. Furthermore, as industries focus on reducing waste and improving sustainability, there is a growing demand for cutting tools that offer longer tool life and lower energy consumption. This shift presents an opportunity for tool manufacturers to innovate and develop eco-friendly products that cater to the evolving needs of the market.
Additionally, the expansion of electric and hybrid vehicle production presents a unique opportunity for high feed milling tool manufacturers to develop specialized tooling solutions tailored for these applications. The automotive industry's transition towards electrification requires advanced machining techniques and materials that can accommodate the specific requirements of electric vehicle components. As manufacturers in this sector prioritize efficiency and precision, the demand for high-performance high feed milling tools is likely to increase. Moreover, the growing trend of outsourcing machining processes to specialized manufacturers can also create opportunities for tool manufacturers to establish partnerships and expand their market reach.
Threats
Despite the promising outlook for the High Feed Milling Tools market, several threats could potentially hinder growth. One of the most significant challenges is the fluctuating prices of raw materials used in the production of high feed milling tools. Variability in the costs of carbide, steel, and other essential materials can impact profit margins and pricing strategies for manufacturers. Additionally, the market is highly competitive, with numerous players vying for market share, leading to price wars that may affect the profitability of established companies. As manufacturers strive to differentiate themselves through innovation and quality, the pressure to continuously invest in research and development can pose financial challenges, particularly for smaller companies.
Another potential threat to the market is the rapid pace of technological advancements in machining processes. As new technologies emerge, manufacturers may need to continuously adapt their products to meet evolving industry standards and customer demands. Failure to keep up with these advancements may result in obsolescence and loss of market share. Moreover, the ongoing global economic uncertainties and potential trade restrictions can also impact the supply chains and distribution networks of high feed milling tools, further complicating the market landscape. Manufacturers must remain vigilant and adaptable to navigate these challenges effectively.
Competitor Outlook
- Kennametal Inc.
- Sandvik Coromant
- Walter AG
- Seco Tools
- MSC Industrial Direct Co., Inc.
- Gühring KG
- HORN Group
- Kyocera Corporation
- Iscar Ltd.
- OSG Corporation
- Emuge-Franken
- Sumitomo Electric Industries, Ltd.
- Mapal GmbH
- Fette Compacting GmbH
- Accuway Tooling Co., Ltd.
The competitive landscape of the High Feed Milling Tools market is characterized by the presence of several key players who are constantly innovating to maintain their market positions. Companies like Kennametal Inc. and Sandvik Coromant have established themselves as leaders in high-performance tooling solutions, leveraging their extensive research and development capabilities to introduce advanced high feed milling tools that meet the evolving demands of various industries. Their comprehensive product portfolios and commitment to quality assurance have enabled them to build strong relationships with customers, thereby enhancing their competitive edge.
Another noteworthy player, Walter AG, is recognized for its innovative approach to high feed milling tools, focusing on specialized solutions for complex machining processes. The company's dedication to advancing cutting tool technology through continuous investment in R&D has resulted in a range of high-performance products tailored for specific applications. Furthermore, Seco Tools and MSC Industrial Direct Co., Inc. are also significant contributors to the market, offering a diverse range of high feed milling tools that cater to different machining needs across various industries.
Moreover, Gühring KG and HORN Group are noteworthy competitors that excel in providing high-quality cutting tools for diverse applications. Their emphasis on precision engineering and commitment to customer satisfaction has established them as reliable partners in the machining industry. Additionally, the emergence of companies like Kyocera Corporation and Iscar Ltd. has intensified the competition in the market, as they bring innovative solutions and cutting-edge technologies that continuously reshape the landscape of high feed milling tools. As the market evolves, these companies will likely engage in strategic collaborations, mergers, and acquisitions to enhance their market presence and drive growth.
1 Appendix
- 1.1 List of Tables
- 1.2 List of Figures
2 Introduction
- 2.1 Market Definition
- 2.2 Scope of the Report
- 2.3 Study Assumptions
- 2.4 Base Currency & Forecast Periods
3 Market Dynamics
- 3.1 Market Growth Factors
- 3.2 Economic & Global Events
- 3.3 Innovation Trends
- 3.4 Supply Chain Analysis
4 Consumer Behavior
- 4.1 Market Trends
- 4.2 Pricing Analysis
- 4.3 Buyer Insights
5 Key Player Profiles
- 5.1 Walter AG
- 5.1.1 Business Overview
- 5.1.2 Products & Services
- 5.1.3 Financials
- 5.1.4 Recent Developments
- 5.1.5 SWOT Analysis
- 5.2 HORN Group
- 5.2.1 Business Overview
- 5.2.2 Products & Services
- 5.2.3 Financials
- 5.2.4 Recent Developments
- 5.2.5 SWOT Analysis
- 5.3 Iscar Ltd.
- 5.3.1 Business Overview
- 5.3.2 Products & Services
- 5.3.3 Financials
- 5.3.4 Recent Developments
- 5.3.5 SWOT Analysis
- 5.4 Mapal GmbH
- 5.4.1 Business Overview
- 5.4.2 Products & Services
- 5.4.3 Financials
- 5.4.4 Recent Developments
- 5.4.5 SWOT Analysis
- 5.5 Seco Tools
- 5.5.1 Business Overview
- 5.5.2 Products & Services
- 5.5.3 Financials
- 5.5.4 Recent Developments
- 5.5.5 SWOT Analysis
- 5.6 Emuge-Franken
- 5.6.1 Business Overview
- 5.6.2 Products & Services
- 5.6.3 Financials
- 5.6.4 Recent Developments
- 5.6.5 SWOT Analysis
- 5.7 Kennametal Inc.
- 5.7.1 Business Overview
- 5.7.2 Products & Services
- 5.7.3 Financials
- 5.7.4 Recent Developments
- 5.7.5 SWOT Analysis
- 5.8 OSG Corporation
- 5.8.1 Business Overview
- 5.8.2 Products & Services
- 5.8.3 Financials
- 5.8.4 Recent Developments
- 5.8.5 SWOT Analysis
- 5.9 Sandvik Coromant
- 5.9.1 Business Overview
- 5.9.2 Products & Services
- 5.9.3 Financials
- 5.9.4 Recent Developments
- 5.9.5 SWOT Analysis
- 5.10 Gühring KG
- 5.10.1 Business Overview
- 5.10.2 Products & Services
- 5.10.3 Financials
- 5.10.4 Recent Developments
- 5.10.5 SWOT Analysis
- 5.11 Kyocera Corporation
- 5.11.1 Business Overview
- 5.11.2 Products & Services
- 5.11.3 Financials
- 5.11.4 Recent Developments
- 5.11.5 SWOT Analysis
- 5.12 Fette Compacting GmbH
- 5.12.1 Business Overview
- 5.12.2 Products & Services
- 5.12.3 Financials
- 5.12.4 Recent Developments
- 5.12.5 SWOT Analysis
- 5.13 Accuway Tooling Co., Ltd.
- 5.13.1 Business Overview
- 5.13.2 Products & Services
- 5.13.3 Financials
- 5.13.4 Recent Developments
- 5.13.5 SWOT Analysis
- 5.14 MSC Industrial Direct Co., Inc.
- 5.14.1 Business Overview
- 5.14.2 Products & Services
- 5.14.3 Financials
- 5.14.4 Recent Developments
- 5.14.5 SWOT Analysis
- 5.15 Sumitomo Electric Industries, Ltd.
- 5.15.1 Business Overview
- 5.15.2 Products & Services
- 5.15.3 Financials
- 5.15.4 Recent Developments
- 5.15.5 SWOT Analysis
- 5.1 Walter AG
6 Market Segmentation
- 6.1 High Feed Milling Tools Market, By Application
- 6.1.1 Aerospace
- 6.1.2 Automotive
- 6.1.3 Die & Mold
- 6.1.4 General Machining
- 6.1.5 Medical
- 6.2 High Feed Milling Tools Market, By Product Type
- 6.2.1 Solid Carbide High Feed Milling Tools
- 6.2.2 Indexable High Feed Milling Tools
- 6.2.3 HSS High Feed Milling Tools
- 6.2.4 Ceramic High Feed Milling Tools
- 6.2.5 Diamond High Feed Milling Tools
- 6.3 High Feed Milling Tools Market, By Material Type
- 6.3.1 Carbide
- 6.3.2 High-Speed Steel
- 6.3.3 Cermet
- 6.3.4 Ceramic
- 6.3.5 Diamond
- 6.4 High Feed Milling Tools Market, By Distribution Channel
- 6.4.1 Direct Sales
- 6.4.2 Indirect Sales
- 6.1 High Feed Milling Tools Market, By Application
7 Competitive Analysis
- 7.1 Key Player Comparison
- 7.2 Market Share Analysis
- 7.3 Investment Trends
- 7.4 SWOT Analysis
8 Research Methodology
- 8.1 Analysis Design
- 8.2 Research Phases
- 8.3 Study Timeline
9 Future Market Outlook
- 9.1 Growth Forecast
- 9.2 Market Evolution
10 Geographical Overview
- 10.1 Europe - Market Analysis
- 10.1.1 By Country
- 10.1.1.1 UK
- 10.1.1.2 France
- 10.1.1.3 Germany
- 10.1.1.4 Spain
- 10.1.1.5 Italy
- 10.1.1 By Country
- 10.2 Asia Pacific - Market Analysis
- 10.2.1 By Country
- 10.2.1.1 India
- 10.2.1.2 China
- 10.2.1.3 Japan
- 10.2.1.4 South Korea
- 10.2.1 By Country
- 10.3 Latin America - Market Analysis
- 10.3.1 By Country
- 10.3.1.1 Brazil
- 10.3.1.2 Argentina
- 10.3.1.3 Mexico
- 10.3.1 By Country
- 10.4 North America - Market Analysis
- 10.4.1 By Country
- 10.4.1.1 USA
- 10.4.1.2 Canada
- 10.4.1 By Country
- 10.5 Middle East & Africa - Market Analysis
- 10.5.1 By Country
- 10.5.1.1 Middle East
- 10.5.1.2 Africa
- 10.5.1 By Country
- 10.6 High Feed Milling Tools Market by Region
- 10.1 Europe - Market Analysis
11 Global Economic Factors
- 11.1 Inflation Impact
- 11.2 Trade Policies
12 Technology & Innovation
- 12.1 Emerging Technologies
- 12.2 AI & Digital Trends
- 12.3 Patent Research
13 Investment & Market Growth
- 13.1 Funding Trends
- 13.2 Future Market Projections
14 Market Overview & Key Insights
- 14.1 Executive Summary
- 14.2 Key Trends
- 14.3 Market Challenges
- 14.4 Regulatory Landscape
Segments Analyzed in the Report
The global High Feed Milling Tools market is categorized based on
By Product Type
- Solid Carbide High Feed Milling Tools
- Indexable High Feed Milling Tools
- HSS High Feed Milling Tools
- Ceramic High Feed Milling Tools
- Diamond High Feed Milling Tools
By Application
- Aerospace
- Automotive
- Die & Mold
- General Machining
- Medical
By Distribution Channel
- Direct Sales
- Indirect Sales
By Material Type
- Carbide
- High-Speed Steel
- Cermet
- Ceramic
- Diamond
By Region
- North America
- Europe
- Asia Pacific
- Latin America
- Middle East & Africa
Key Players
- Kennametal Inc.
- Sandvik Coromant
- Walter AG
- Seco Tools
- MSC Industrial Direct Co., Inc.
- Gühring KG
- HORN Group
- Kyocera Corporation
- Iscar Ltd.
- OSG Corporation
- Emuge-Franken
- Sumitomo Electric Industries, Ltd.
- Mapal GmbH
- Fette Compacting GmbH
- Accuway Tooling Co., Ltd.
- Publish Date : Jan 21 ,2025
- Report ID : IN-42386
- No. Of Pages : 100
- Format : |
- Ratings : 4.5 (110 Reviews)
Related reports
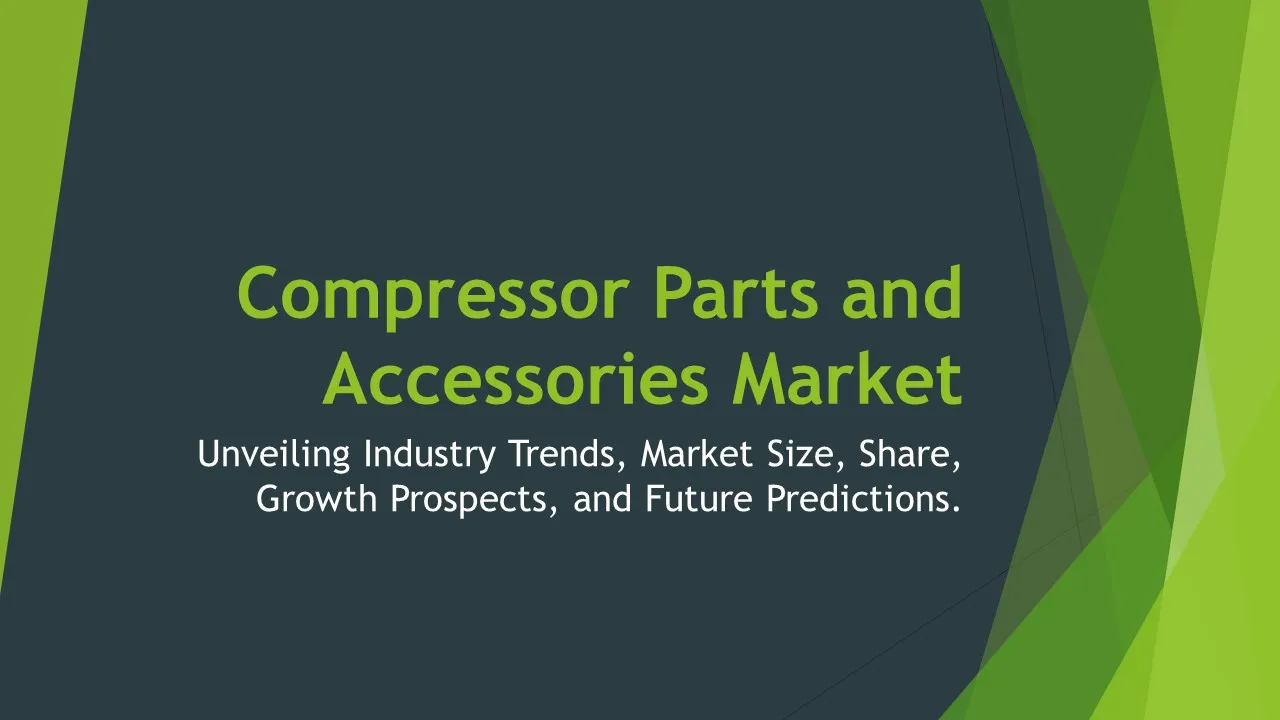
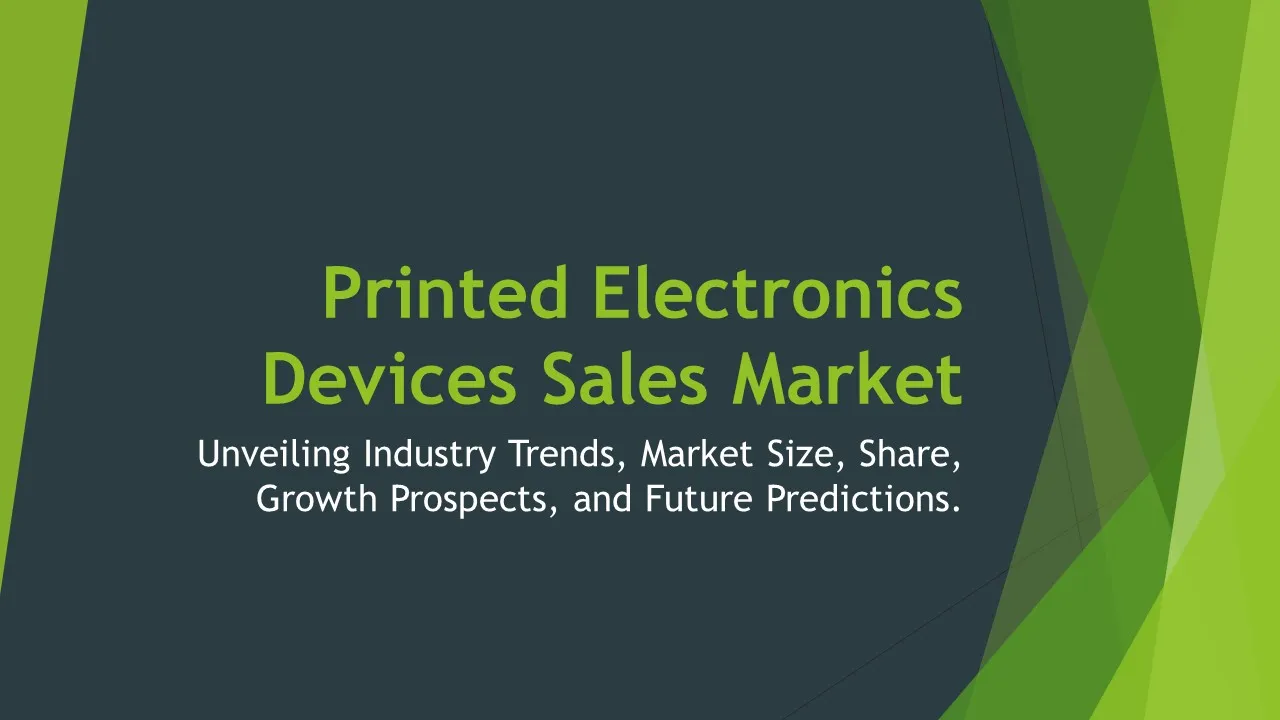